LABCOAT
10
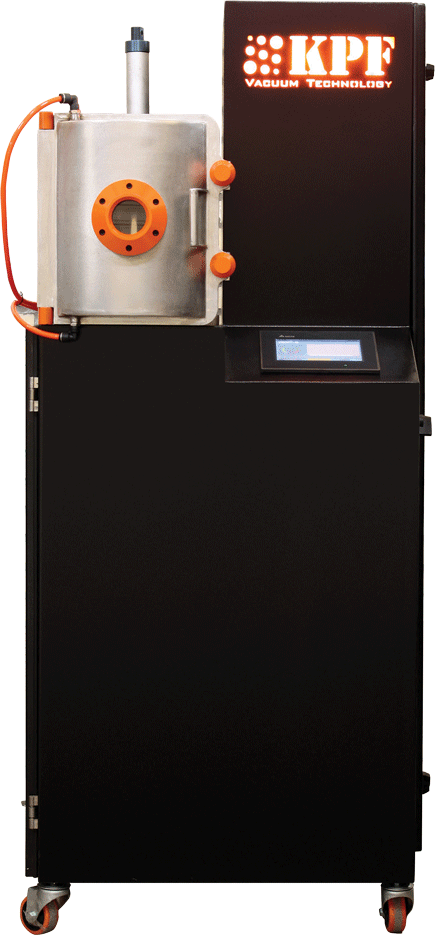
Multi-purpose vacuum coating system
Applications
Multi-purpose vacuum coating machine with magnetron sputtering technology enables the evaporation of wide range of materials and deposition on many substrates with different materials. This machine is designed to easily set up another types of evaporation sources, advanced deposition accessories and equipment.
- 10 liters double-walled water-cooled stainless steel vacuum chamber with front door for ease of use equipped to door sensor and self-locked system and excess standard ports to upgrade system (addition of evaporation sources and other optional equipment)
- Ergonomic chassis with electrostatic painting and easy access to various parts of machine (easy maintenance and promotion)
- Vacuum degree: 5*10-5 mbar
- Vacuum system including rotary and diffusion pumps and other high-vacuum accessories (Pirani gauge, Penning gauge, vacuum valves and so on)
- Water-cooled 2 inch magnetron sputtering source with easy installation
- DC power supply
- Automatic shutter on magnetron sputtering source
- Mass Flow Control (MFC) connected to central control system
- Sample holder system
- PLC central control system along with all necessary protections and sensors
- Touch screen with data storage and recovery
- Excess ports to set up various systems in the roof and back of chamber
- The possibility of installing substrate heater up to 300 oC due to metallic and double-walled chamber
- The possibility of installing crystal thickness gauge sensor
- The possibility of installing sample rotating system (simple or planetary rotation)
- The possibility of installing various evaporation sources and connection to central control system
- Easy accessibility for placing and fixing the mold
- Pulsed DC power supply with accurate adjustable pulse width on/off (ms 780…1)
- Increasing heating rate up to 1000 oC/min
- Ability to set all sintering parameters
- Programmable sintering cycle
- Fully automatic control of system with programmable central controller and all necessary safeties
- Commanding and monitoring with touchscreen
- Cooling system to protect the sealing and packing at elevated temperatures