The development of modern materials such as high-performance ceramics often relies on computational predictions as a valuable tool in accelerating the discovery process. It is essential to experimentally confirm the material properties of such predictions
“Unfortunately, the screening rates of predicted materials are limited by the long processing times and poor compositional control from volatile element loss in conventional ceramic sintering techniques,” Liangbing Hu, the Minta Martin Professor in the Department of Materials Science and Engineering at the University of Maryland, tells Nanowerk. “For instance, during our solid state battery research, we encountered the massive challenge posed by conventional sintering methods on fabricating solid state electrolytes due to the prolonged sintering process, severe volatile element loss, high porosity, and poor composition integration.”
He points out that the poor property of the solid state electrolytes (SSEs) results in the inferior electrochemical performance of the battery. To overcome these limitations, Hu’s team developed an ultrafast high-temperature sintering (UHS) technique to fabricate SSEs with dense structure and excellent electrochemical performance.
To conduct the process, the researchers sandwich a pressed green pellet of ceramic precursor powders between two Joule-heating carbon strips that rapidly heat the pellet through radiation and conduction to form a uniform high-temperature environment for quick synthesis (solid-state reaction) and reactive sintering. In an inert atmosphere, these carbon heating elements can provide a temperature of up to 3000 °C, which is sufficient to synthesize and sinter virtually any ceramic material. Comparing their new synthesis method with key parameters of conventional rapid sintering methods, the UHS technique has a much higher heating rate and cooling rate; requires much less sintering time (1–10 seconds); can reach a temperature of up to 3000 °C, and features minimal sample requirements, making it a general sintering method. Additionally, the UHS technique enables the realization of 3D printing structures and co-sintering of multilayer structures
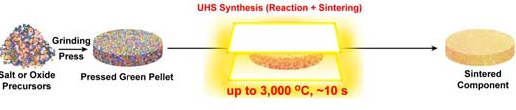
source